The manufacturing process involves many operations and takes multiple employees to complete the job correctly and create the perfect end product. The moving parts of the machinery and its operations must be evaluated regularly to determine if changes become necessary. Maximizing performance begins with simplifying the procedures and creating a streamlined approach whenever possible.
How Can Manufacturers Use Ball Screw Assemblies to Improve Operations?
Manufacturers must consider every avenue when learning How to Simplify a Manufacturing Processes. Ball screw assemblies offer a much higher level of efficiency, speed, frictionless operation, and quiet than lead screws, pneumatic screws, and hydraulic options. Companies adopting ball screw assemblies see less downtime and improve their bottom lines because they do not have to replace these assembles as frequently, given their strong performance and protection levels.
Other Tips for Helping Improve the Manufacturing Process
Employers who want to see success in their day-to-day operations must be willing to adapt to the ever-changing industry standards and supply their employees with the tools and equipment necessary for the job. With so many processes involved in manufacturing, it is no surprise that many companies struggle with simplification. Manufacturers must consider the following tips.
Workplace Organization Is Critical
One of the most significant impairments to simplification is a lack of organization. Unorganized companies have no specific place for tools and equipment, leaving employees struggling to leave their workstations to find what they need to perform their jobs. Employers must organize their manufacturing floors and give employees easy access to what they need. Improved downtime and reduced employee aggravation are two improvements that come about as a result of workplace organization. Not only must the employer initiate the organization, but they must also follow up regularly to ensure everyone is doing their part to stay organized.
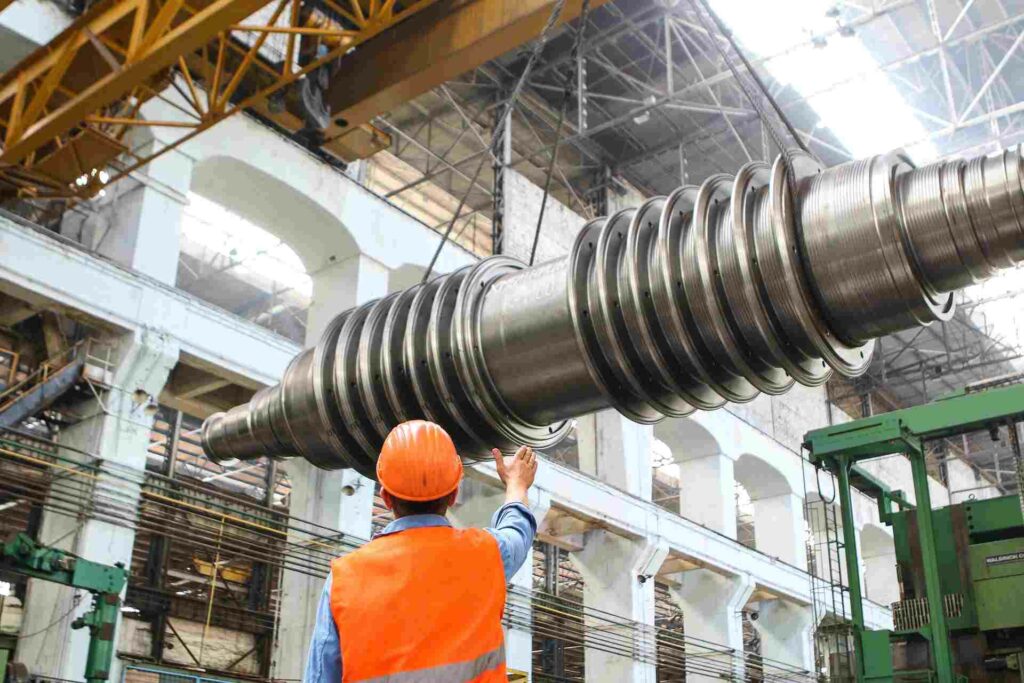
Identify Weaknesses in the Workforce
Employers must match employee strengths with applicable job duties. Doing so reduces mistakes and improves employee morale. Employees are more likely to stay in a position they feel confident performing. Overcoming weaknesses in the workforce is critical for day-to-day operations. Employers can overcome employee weaknesses by implementing training programs. These programs encourage employees to strive for their best work and help eliminate confusion in their jobs.
Coordinate Departments
Many employers find it challenging to coordinate their departments due to a lack of communication. Coordination involves bringing every department on the same page, regardless of their operation responsibilities. Ideally, companies should adopt software programs that give a central access point for all employees to view the data they need. Coordinating departments begins with keeping everyone informed through regular company meetings that foster communication among the various departments.
Get Started Right Away
In addition to the above, manufacturers must survey their operational equipment to ensure it is in sound shape and operating efficiently. Minor changes to equipment, such as switching to ball screw assemblies, can offer welcome improvements in day-to-day operations. Employers who remain actively involved with their employees and seek feedback are likelier to see improved functions that will pay off in the long run and improve their manufacturing processes.